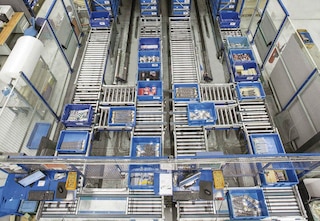
Définition et fonctionnement de la méthode Kanban en logistique
La méthode Kanban organise l'approvisionnement et la production de biens lorsque les processus de fabrication fonctionnent selon la méthode du juste-à-temps (JAT), qui consiste à se faire livrer les matières premières au moment exact du besoin. L'objectif final est d'ajuster la capacité de production à la demande afin d'éviter le surstock et les temps d'attente inutiles entre les processus.
Créé dans les années cinquante par la société japonaise Toyota, le système Kanban s’inscrit dans le cadre de la méthodologie Lean manufacturing (visant à minimiser les déchets pour augmenter la productivité). Inventé par l'ingénieur industriel Taiichi Ohno, ce modèle de production s'est révélé être la solution pour faire face à la profonde dépression dans laquelle s'était enfoncée l'industrie japonaise suite à la Seconde Guerre Mondiale.
Qu'est-ce que le système Kanban ? Définition et origine
La méthode Kanban établit un protocole pour le réapprovisionnement des stocks. Il s'agit d'un système de communication des ordres de fabrication et d'approvisionnement en matériaux. Il est utilisé dans les modèles de production qui répondent de manière directe à la demande (flux tirés : la fabrication du produit ne commence que lorsque l'usine de production reçoit la commande ferme du client).
Taiichi Ohno a conçu le système Kanban en s'inspirant des règles de réapprovisionnement des supermarchés américains. Dans ces magasins, les clients retirent les produits étiquetés des rayons et, en passant en caisse, le système recueille toutes les références vendues et émet un ordre de réapprovisionnement à l'entrepôt, qui identifie les marchandises de la même manière. Une fois les articles réassortis dans le supermarché, l'entrepôt envoie à son tour un ordre de réapprovisionnement à ses fournisseurs ou fabricants, et ainsi de suite tout au long de la Supply Chain. Le système de point de commande est utilisé afin de déterminer le moment où déclencher les ordres de réapprovisionnement.
Comment cela fonctionne-t-il ? Les étiquettes et tableaux Kanban
En japonais, Kanban signifie littéralement « cartes de couleurs ». À l'origine, des fiches cartonnées étaient utilisées pour solliciter au processus précédent les pièces nécessaires. Une fois l'ordre de réapprovisionnement exécuté, la carte Kanban retournait dans son casier original.
Ces cartes ou étiquettes reprenaient les informations identifiant chaque lot de matériel : SKU, code, taille du lot, destination de la marchandise, client à l’origine de la demande, etc. Les étiquettes étaient accrochées à chaque conteneur, ou étagère, où se trouvait le produit.
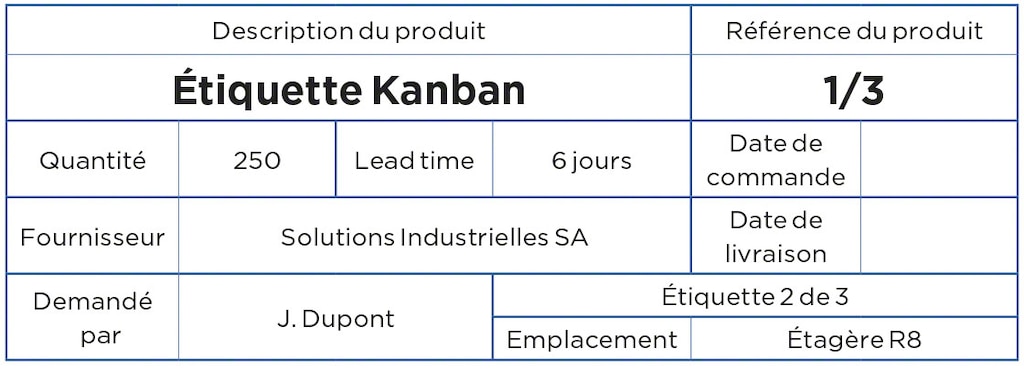
Aujourd'hui, le système Kanban a été remplacé par des applications informatiques chargées de mettre en marche le processus de réapprovisionnement. Le système de travail peut également être représenté par des tableaux Kanban formés de plusieurs colonnes où sont placées les cartes ou étiquettes virtuelles. De cette manière, chaque colonne indique le statut de chaque tâche et la personne responsable de son exécution.
Bien qu'à l'origine la méthode Kanban soit apparue dans un contexte industriel, elle est actuellement appliquée à la gestion de tout type de projets, notamment le développement de logiciels.
Les types d'étiquettes Kanban
Il existe principalement deux types d'étiquettes Kanban :
- Kanban de manutention ou de transport : cette étiquette indique la quantité de produits devant être réapprovisionnée pour répondre aux besoins de l'échelon suivant de la Supply Chain. Si nous prenons l'exemple d'un supermarché, l'étiquette Kanban de transport serait utilisée pour indiquer qu'un produit a été vendu et qu'il doit être transféré de l'entrepôt vers le linéaire du magasin.
- Kanban de production : elle est utilisée pour demander la fabrication d'un produit. Si nous reprenons le même exemple, ce type d'étiquette Kanban serait émis par l'entrepôt en cas de rupture de stock (parce que les produits auraient déjà été envoyés en magasin).
Le diagramme suivant présente de manière schématique le fonctionnement en chaîne des cartes Kanban de production et de transport sur une ligne de production simplifiée :
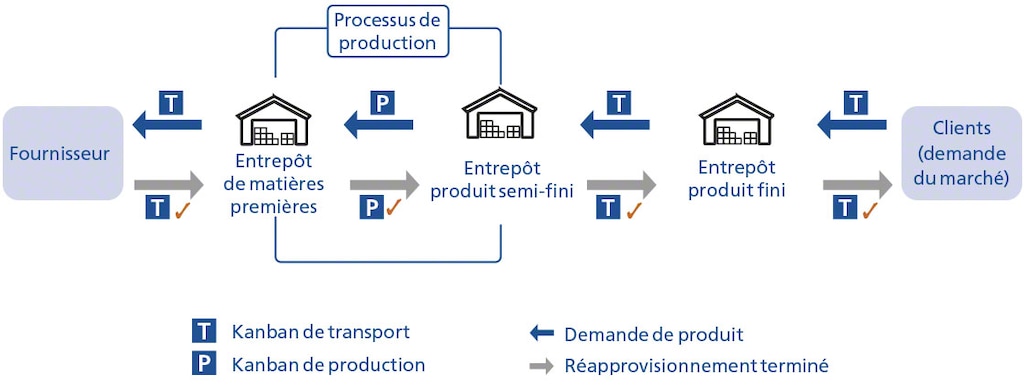
Les avantages du système Kanban en logistique et en production
La méthode Kanban est le parfait allié du système juste-à-temps car elle permet de :
- visualiser l’état d’avancement du travail et d'identifier facilement chaque phase du cycle de production ou de réapprovisionnement;
- fixer facilement les limites du travail en cours (également appelé WIP, work in progress) afin d'éviter la formation de goulots d'étranglement;
- mesurer le lead time entre les processus, c'est-à-dire le temps nécessaire à la réalisation de chaque phase;
- contrôler la production et les matériaux disponibles dans les différentes installations de stockage;
- éviter la surproduction ou l'excès de stock ce qui représente un gain d'espace de stockage.
Les inconvénients de l'utilisation du système Kanban
Cette méthode n’est pas toujours la plus adéquate car elle présente certaines restrictions.
- Le système Kanban donne des résultats optimaux lorsque le flux de production est distribué uniformément tout au long de l'année et qu’il est organisé en courtes séries de volumes semblables. En revanche, si l'entreprise est soumise à une forte volatilité de la demande qui exige des ajustements brusques de la production, la méthode Kanban comporte des limites et son utilisation est donc déconseillée.
- Si l'un des échelons de la chaîne de production rencontre un problème, cette méthode risque d'aggraver les retards.
- Ce système n’est pas le plus flexible pour faire face aux changements importants des techniques de fabrication des produits.
- Il ne fonctionne pas correctement si les fournisseurs ne suivent pas les mêmes règles Kanban pour le réapprovisionnement.
Quand utiliser Kanban dans un entrepôt ? Le rôle du WMS
Dans les entrepôts, la méthode Kanban ne fait désormais plus l’usage de fiches cartonnées : les entreprises l'emploient désormais par le biais d'un système de gestion d'entrepôt (tel qu'Easy WMS) associé à des systèmes d'identification automatique tels que les codes-barres ou la RFID. Chaque enregistrement dans le WMS fonctionne comme une étiquette Kanban car, lorsque les données sont lues par un scanner, le système renvoie toutes les informations liées à ce SKU.
En logistique, cette méthode s’emploie pour organiser le réapprovisionnement de stock à différents niveaux :
Kanban dans un seul et même entrepôt
Si les adressages dédiés au picking et ceux de stockage sont divisés, le système Kanban est particulièrement utile pour réapprovisionner les stocks des rayonnages de picking.
Lorsque les références de ces emplacements de picking sont épuisées, le WMS émet un avertissement automatique de réapprovisionnement qui fonctionne comme une étiquette Kanban. Lorsqu'un opérateur détecte un manque de matériel, il peut également l'activer manuellement.
De cette manière, le changement d'emplacement de marchandises est programmé en fonction de la priorité, bien qu'il soit généralement réservé aux heures creuses de l’entrepôt (c'est par exemple le cas du picking par vagues ou wave picking).
Si lors du transfert de marchandises de la zone de stockage à la zone de picking, on observe que des références sont également épuisées dans la zone de stockage, le WMS peut envoyer une notification directe au département d'achats afin qu'il en tienne compte en transmettant les commandes aux fournisseurs.
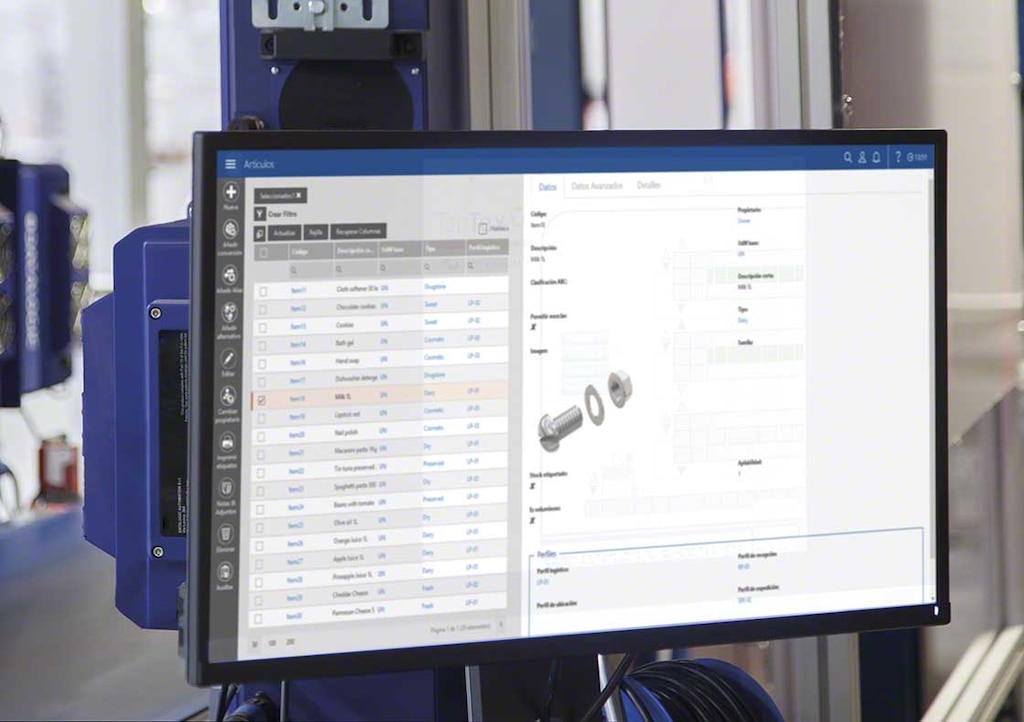
Kanban dans un réseau d'entrepôts logistiques
La méthode Kanban peut également s'appliquer aux entreprises qui travaillent avec un stock réparti dans plusieurs entrepôts. Ces derniers peuvent servir une même ligne de production (comme en logistique de production) ou faire partie d'un même réseau logistique (comme dans les réseaux logistiques du secteur retail).
Voici le fonctionnement du système Kanban dans chacun de ces cas et les fonctions remplies par le WMS :
- Application du système Kanban dans les entrepôts de production : les entrepôts qui fournissent les usines gèrent des stocks classés par matières premières, produits semi-finis et finis. Pour contrôler qu'aucune rupture de stock ne survient lors des processus de production, il est essentiel de maintenir un contrôle de stock informatisé. Le WMS pour la production travaille selon la méthode Kanban car, face à une nouvelle commande, le WMS émet, d’une part, des ordres de fabrication et contrôle, d’autre part, le stock de sécurité disponible pour chaque référence.
- Application du système Kanban dans les Supply Chain du secteur retail : dans ce cas, le réseau logistique est formé par des entrepôts (centraux et régionaux) et des magasins physiques. En suivant la méthode Kanban, la demande des produits est enregistrée dans le point de vente d'où sont émis les ordres de réapprovisionnement des entrepôts. Dans ce cas, le WMS agit comme un catalyseur de réapprovisionnement entre les centres car il contient les données globales de stock. Par ailleurs, si nous prenons l'exemple d'Easy WMS de Mecalux, le module Store Fulfillment permet d'organiser et de classer, sans intermédiaires, les flux de stocks entre les centres et ainsi d'exploiter au mieux la capacité logistique de l'entreprise.
Gestion des stocks avec la méthode Kanban
L'application du système Kanban traditionnel avec des stocks de taille considérable, répartis entre différents centres, en gérant un volume de SKU particulièrement élevé, s'avère inefficace en raison de la complexité croissante du secteur. Toutefois, il est possible de planifier le réapprovisionnement des stocks et de profiter des avantages de cette méthode à l'aide d'un WMS.
Easy WMS dispose de fonctions de gestion de stock intégrée avancées et permet de travailler avec différentes règles de réapprovisionnements. Si vous souhaitez plus d’informations sur le fonctionnement de notre WMS, contactez-nous. L’un de nos spécialistes vous expliquera en détail la manière dont ce logiciel peut contribuer à la gestion optimisée de votre entrepôt.