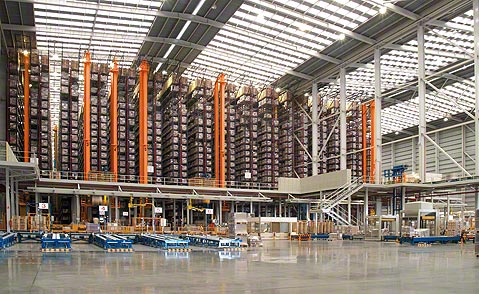
Mecalux finalise avec succès le processus d’automatisation des entrepôts de Porcelanosa Grupo
Le plus grand centre logistique céramique du monde au service de Porcelanosa
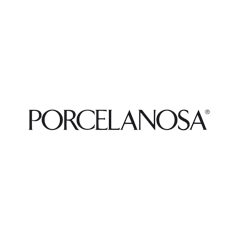
Avec l’inauguration du centre logistique pour l’entreprise de revêtements de sols Venís, Porcelanosa Grupo a finalisé son ambitieux plan d’agrandissement et de modernisation de ses centres de stockage entamé en 2003. Pendant ces années, le groupe d’entreprises espagnol a confié à Mecalux l’automatisation des 5 centres logistiques de son siège de Villareal, considérée comme un enjeu stratégique pour soutenir la croissance des entreprises du groupe dans le monde entier.
Besoins du client
Porcelanosa Grupo, formé par 8 entreprises leaders dans leur secteur respectif et présent dans plus de 100 pays, fait partie des entreprises espagnoles qui bénéficient d’une notoriété et d’une implantation au niveau international.
Étant donné les perspectives de croissance du groupe et une Direction convaincue que le stockage et la manipulation du produit fini sont essentiels pour se forger un avantage compétitif, la société s’est lancée au début de ce nouveau siècle dans l’automatisation de ses cinq centres logistiques situés à son siège de Villareal : Porcelanosa, puis ceux des entreprises Ceranco, L’Antic Colonial, Noken et finalement en 2012, celui de Venís, référence dans la fabrication et la conception de carrelage design et de porcelaine.
Les entrepôts du groupe ont été conçus en étroite collaboration avec Mecalux, qui a tenu compte dans chaque cas des besoins divers et des caractéristiques du produit.
Le centre logistique réalisé pour Venís devait finaliser le processus de modernisation et contribuer à réaliser l’un des objectifs du groupe : atteindre une capacité de 275 000 palettes. Un autre objectif consistait à relier l’installation de production de Venís à son centre logistique, éliminant ainsi les coûts de transport et facilitant le déplacement des produits. Afin d’y parvenir, Mecalux a mis en place les solutions de stockage les plus innovantes et efficaces à toutes les phases du processus : réception, stockage, picking et expéditions.
Le résultat est un entrepôt totalement automatisé de 7 000 m2 et d’une capacité de plus de 65 000 palettes, qui se traduit par une augmentation notable de la vitesse des entrées et sorties des marchandises.
Solution proposée par Mecalux
Pour les besoins de l’entreprise Venís, Mecalux a construit un bâtiment de 32 mètres de hauteur et 278 mètres de longueur. L’espace y est divisé en plusieurs zones coordonnées par le logiciel de gestion d’entrepôts Easy WMS de Mecalux, qui permet de gérer les différents processus ainsi que le suivi et le contrôle de toutes les références de l’entreprise.
Zone de réception :
Le cycle commence avec le transport des palettes de produit fini, transportées du centre de production jusqu’au silo via un tunnel souterrain long de plus de 1 km et équipé de convoyeurs. Arrivées au silo, les palettes sont levées jusqu’au sommet de l’entrepôt par des élévateurs doubles pouvant charger deux palettes pesant jusqu’à 1 600 kg chacune. Outre l'entrée par le tunnel, l'entrepôt dispose d'une entrée auxiliaire pour les palettes provenant d'autres centres.
Une fois au sommet de l’entrepôt, les palettes passent sur les convoyeurs à rouleaux et à chaînes jusqu’au poste d’identification, où le logiciel Easy WMS contrôle les éventuels incidents. À ce stade, chaque palette est mesurée et pesée, pour s’assurer de son parfait état.
Zone de stockage ou silo :
L’espace de stockage prévu est structuré en 10 allées de 1,75 m de largeur dans lesquelles circulent 10 transtockeurs à deux colonnes qui desservent 20 rayonnages de 31 mètres de hauteur. Ces transtockeurs se déplacent très rapidement dans les allées (jusqu’à 180 m/min) et sont capables de lever les palettes à une vitesse de 48 m/min. Ils disposent les chargements de manière stratégique dans les alvéoles disponibles suivant les ordres du logiciel Easy WMS. Les transtockeurs peuvent exécuter jusqu’à 237 cycles combinés par heure.
La marchandise au taux de rotation le plus élevé est placée dans la partie la plus proche possible du début de l'allée.
L’une des caractéristiques des transtockeurs est leur efficience énergétique, puisqu’ils sont capables de récupérer pour l’autoconsommation une valeur moyenne de 15 % de l’énergie consommée, respectant ainsi l’engagement écologique de l’entreprise tout en veillant à l’économie de coûts correspondante.
Mecalux a également prévu la croissance de l’entreprise et conçu l’entrepôt en réservant suffisamment de place pour un éventuel agrandissement futur, qui permettrait d’installer 5 nouveaux transtockeurs.
Zone de picking :
Pour l'expédition des marchandises, Mecalux a également dû mettre en œuvre des solutions spécifiques, à la fois pour la zone de picking plus complexe, et pour la zone de manipulation des palettes complètes.
Dans la zone de picking, huit postes de travail ont été aménagés, permettant de préparer un total de 31 commandes simultanément. Easy WMS gère également la préparation et l'expédition, des commandes et permet de réaliser quatre commandes simultanément par poste de picking.
Dans cette zone, l’ergonomie et la prévention des risques ont fait l’objet d’une attention spéciale. Ainsi, les mouvements et les processus ont été facilités par l’installation de bras pneumatiques qui permettent aux opérateurs de manipuler le chargement sans efforts. D’autre part, les tables de picking ont été équipées de systèmes hydrauliques qui permettent de les ajuster en hauteur, ce qui améliore la position des opérateurs.
Enfin, deux navettes doubles parcourent les allées de picking et distribuent les commandes complètes sur les tables de sortie.
Zone d’expédition :
Un tunnel facilitant la circulation rapide et en toute sécurité du personnel entre la zone de picking et celle des expéditions a été construit pour relier les deux zones de travail et éviter la zone de circulation des navettes.
La zone d’expédition est aménagée en deux espaces pour le service des palettes complètes et deux autres pour le dépôt des commandes provenant des opérations de picking. Les palettes complètes sont réparties sur six rangées de chaque côté du silo et celles provenant de la zone de picking sont emballées pour ensuite être expédiées.
Avantages pour le client
Avec l’inauguration du centre de stockage pour Venís, Porcelanosa Grupo a finalisé la modernisation des installations de son siège de Villareal, donnant le jour au plus grand centre logistique céramique automatisé du monde. C’est ainsi qu’est réalisé l’objectif d’atteindre une capacité de stockage de 275 000 palettes tout en améliorant l’efficacité et la qualité du service aux clients.
L’installation de transtockeurs, de convoyeurs, d’élévateurs et de navettes, conjointement avec la mise en place du logiciel de gestion d’entrepôt Easy WMS, a permis l’automatisation de tous les processus logistiques et le contrôle parfait de tous les produits. Il en ressort, entre autres, les avantages suivants :
- une productivité améliorée par la multiplication de la vitesse des opérations d’entrée et de sortie des palettes ainsi que des opérations de préparation des commandes ;
- un inventaire en temps réel et une traçabilité maximale ;
- une utilisation optimale de l’espace et une flexibilité pour de futurs agrandissements ;
- une amélioration sensible des conditions de travail, les systèmes robotisés augmentant au maximum la sécurité du travail.
Entrepôt automatique pour palettes | |
---|---|
Longueur des rayonnages :: | 160 m |
Hauteur des rayonnages :: | 42,5 m |
Hauteur des rayonnages :: | 31 m (sous charpente) |
Nb. de rayonnages :: | 20 |
Nb. d’allées :: | 10 |
Largeur de couloir :: | 1 750 mm |
Nb. de transtockeurs :: | 10 |
Nb. de niveaux de charge :: | 23 |
Nb. de modules par rayonnage :: | 71 |
Hauteur des niveaux de charge :: | de 600 à 1 450 mm |
Capacité par alvéole :: | 2 |
Capacité totale :: | 65 320 palettes |
Galerie

L'espace de stockage est entièrement automatisé grâce à 10 transstockeurs à double mât
Demandez conseil à un expert